
ENGINEERING
COST SAVINGS THROUGH INNOVATION
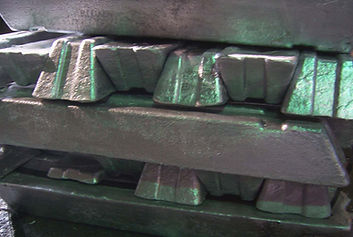
Alloy selection is crucial for obtaining the necessary properties needed for your parts to function as designed. We offer several alloy selections to meet your needs.
AL360 • AL380 • AL383
WHY DIECAST?
The die cast process has many advantages and benefits not achievable with other manufacturing methods.
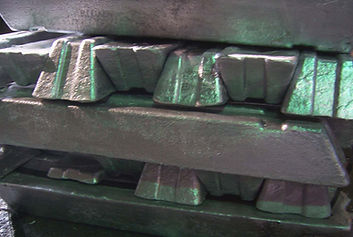
ALLOY SELECTION
MOLD FLOW
ANALYSIS
For critical quality requirements, such as porosity-free castings, we provide assistance through mold flow analysis. The entire gating and metal feeding system is designed and analyzed using advanced computer simulation software. This helps to avoid casting problems by predicting the metal flow, filling characteristics, and solidification of the material. It allows design improvements to be incorporated during the build process, eliminating the expense and time lost in changes made after the tooling is completed.
PROGRESS REPORTING
Following the engineering phase of development, Bardane monitors the die cast tooling construction process through continual communication with our certified tooling suppliers. Our customer is provided with timeline charts throughout the die making process
INSERT MOLDING
Instead of installing as a post process in an assembly, often times we can incorporate an insert in the molding process, saving time and cost for the final product. We can insert materials such as brass, steel, stainless steel, and aluminum. Knurls or grooves are used to secure the insert in place to ensure proper retention.
TOOLING PACKETS
Once die construction is complete, the customer is given a complete set of drawings, along with a tooling guarantee once sample parts are approved. A tooling packet containing steel certifications, heat treat certification, and a complete set of CAD files is provided to the customer as part of each tooling package.
